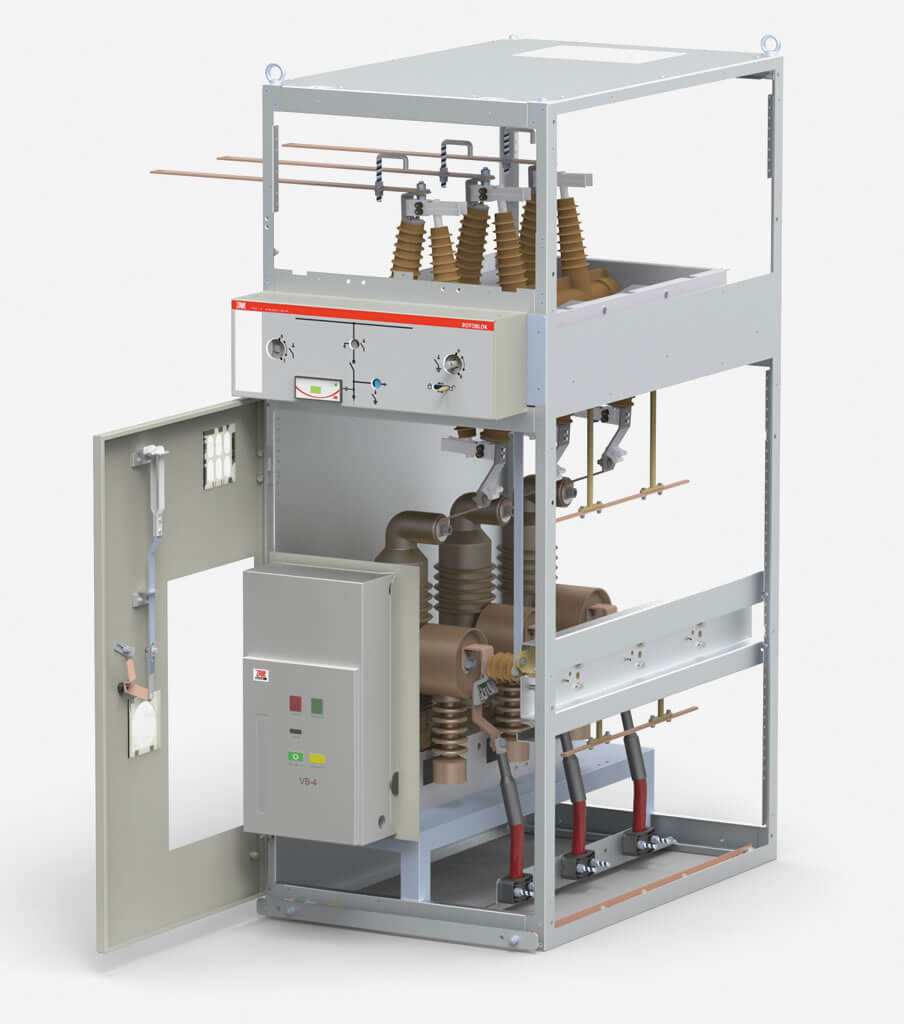
The subject of this document is a ROTOBLOK type state-of-the-art, indoor medium voltage switchgear intended for distribution of three-phase alternating current with a frequency of 50 Hz, at a rated voltage up to 24 kV, in industrial and commercial power sector distribution grids. The switchgears are configured from standard single bays with varied equipment. The information and technical data specified herein enable the designer to assemble a switchgear from typical modules. In case bays with equipment not specified herein or with changed dimensions are needed, the scope of equipment should be arranged with the manufacturer.
Characteristics
The Rotoblok type switchgear is a two compartment, indoors switchgear in metal enclosure made of zinc-coated metal sheet (which ensures equipotential bonding), with a single primary busbars system. The switchgear is equipped with state-of-the-art, air insulated switching devices. It has separate primary busbars and cable compartments, and the arc-proof design ensures high level of operational safety.
The distribution bays have the following properties:
- small external dimensions compared to rated voltage, defined insulation levels, primary busbar rated currents and short-circuit currents,
- two-compartment bay ensuring the separation of the primary busbar circuit from the section used to connect power supply cables,
- high reliability of operation,
- long operating period without the need for troublesome maintenance operations,
- high corrosion resistance, the switchgear design uses metal sheet which has been zinc-coated for corrosion protection,
- universality in designing different switchgear configurations with any number of bays,
- use of state of the art, reliable switching devices, such as GTR type disconnectors and switch disconnectors (ZPUE), or circuit breakers by other manufacturers,
- adapted for the installation of state of the art protection and control devices,
- the possibility of wall-mounting of the switchgear, saving space in the switching room, which is particularly important during retrofits and expansions of existing switching stations,
- easy and quick access to switchgear devices for supervision and maintenance,
- simple operation.
System of interlocks and protections
A system of interlocks prevents incorrect switching operations and opening of the distribution bay doors before voltage is disconnected and the earthing switch is closed. Opening of the earthing switch is possible only when the bay doors are closed (or after the interlock is purposefully released with a special key provided with the switchgear - for example in order to perform a voltage test of a cable). Each feeder bay and circuit breaker bay is equipped as standard with capacitive voltage dividers on each phase and a voltage indicator. Such a solution facilitates checking the cable for lack of voltage and safe phase testing with a phase comparator.
At the customer's request it is possible to provide capacitive voltage dividers in bays which do not have them as standard.
High safety of operation, achieved by:
- arc-proof design - resistance to internal arcing effects,
- specially reinforced bay design (enclosures, locks, hinges),
- mechanical interlocks, which prevent incorrect switching operations and touching live devices,
- access to controlgear and control circuits is possible while the primary circuits parts cannot be touched by the operator,
- the use of monitoring and signalling systems, and mechanical and electrical position indicators, and inspection windows,
- visual indicator of disconnector contacts, switch-disconnector and earthing switch state, and installing of inspection windows to control them,
- possibility of disconnecting the switch disconnector without an operating lever (optional - GTR 2, GTR 2V),
- the use of visible double gap disconnectors and switch disconnectors,
- forcing the sequence of switching operations.
Basic technical data
Compliance with standards:
The Rotoblok type switchgear meets the requirements of the following standards:
- PN-EN62271-1 - “High-voltage switchgear and controlgear. Common specifications”,
- PN-EN 62271-200 - “High-voltage switchgear and controlgear. AC metal-enclosed switchgear and controlgear for rated voltages above 1 kV and up to and including 52 kV”,
- PN-EN 62271-100 - “High-voltage switchgear and controlgear. Alternating-current circuit-breakers”,
- PN-EN 62271-102 - “High-voltage switchgear and controlgear. Alternating current disconnectors and earthing switches”,
- PN-EN 62271-103 - “High-voltage switchgear and controlgear. Switches for rated voltages above 1 kV up to and including 52 kV”,
- PN-EN 62271-105 - “High-voltage switchgear and controlgear. Alternating current switch-fuse combinations”.
The switchgear is certified by the Electrotechnical Institute.
Electrical data: | ||
Rotoblok 17,5kV | Rotoblok 24 | |
Rated network voltage | 15 kV | 20 kV |
Highest device voltage | 17,5 kV | 24 kV |
Rated frequency / number of phases | 50 Hz / 3 | |
Rated short-time network frequency withstand voltage |
55 kV / 63 kV | 50 kV / 60 kV |
Rated withstand lightning surge voltage 1,2/50 μs | 95 kV / 110 kV | 125 kV / 145 kV |
Continuous rated current | 630 A / 1250 A | 630 A - 1250 A |
Rated short-time withstand current | 16 kA (1s) | 16 kA (1s) |
Rated peak withstand current | 40 kA | 40 kA |
IAC internal arc resistance classification | AF up to 16 kA (1s) | |
IP protection rating | IP4X |
Service conditions: | |
Ambient temperature | |
- peak short-time
|
+ 40°C |
- highest day average
|
+ 35°C |
- highest annual average
|
+ 20°C |
- lowest long-term
|
- 25°C1) |
Relative humidity of air | |
- highest day average
|
95% |
- highest month average
|
90% |
- highest day average vapour pressure
|
2,2 kPa |
- highest month average vapour pressure
|
1,8 kPa |
Atmosphere at the place of installation | no significant contamination with salt, vapour, dust, smoke, flammable or corrosive gasses and lack of icing, frosting and dewing |
Installation altitude | up to 1000 m asl2) |
Vibrations | vibrations caused by external factors or earthquakes negligible |
Note:
*1) Unless the manufacturer of instrumentation & control and protection devices has specified otherwise.
*2) If the switchgear installation altitude is higher than 1000 m ASL should corrected by an indicator in accordance with the guidelines of item 2.2.1 of the PN-EN 62271-1 standard.
Rated power of transformers that can be connected and disconnected using GTR 2V disconnectors, depending on voltages on the MV side: | ||
Rated network voltage | Rated current | Max. transformer power |
6 kV | 60,6 A | 630 kVA |
10 kV | 57,7 A | 1000 kVA |
15 kV | 48,1 A | 1250 kVA |
20 kV | 46,2 A | 1600 kVA |
In case of transformers with higher powers please contact the switchgear manufacturer.
In Rotoblok type switchgear typical fuse links are used acc. to the IEC 282-1, DIN 43625 standard, with thermal protection.
Construction of switchgear type Rotoblok
The design of each bay includes elements constructed with zinc-coated metal sheet, and bolted or riveted together. The construction of each bay ensures the possibility of easy assembly in any switchgear unit, and also rapid disassembly (e.g. in order to carry single bays into the station) and custom reconfiguration. Each bay may be constructed wider than its standard dimension. This solution is used when replacing older large size switchgears (e.g. Rue, M20) with a Rotoblok switchgear, when problems may occur with shifting the old cables to a new attachment point.
Each bay has two compartments, that is, the frame and the main disconnector shaft form a mechanical and electrical partition between the lower part of the switchgear and the primary busbar circuit. After opening the bay doors touching the primary busbar circuit is impossible. Each bay is equipped with a lower earthing switch (in a transformer bay it is installed under the fuse bases).
Each bay has a system of mechanical interlocks, which fulfils two primary tasks:
- prevents opening the door of any compartment before its power supply is switched off and the earthing switch is closed; therefore it prevents electric shock,
- forces the proper sequence of the switching operations.
Capacitive voltage dividers used in the bays allow checking for lack of voltage, and safe phase testing from the front side of the bay, in a safe manner, using a LV bipolar indicator without needing to open the bay doors. Additionally, inspection windows installed in the doors allow the observation of each element in the bay, for example: open circuits, condition of transformers, chambers, connections, etc.
An auxiliary circuits compartment is located at the top of the circuit breaker bay, used to install such elements as: terminal strips, relays, batteries, additional (or primary) protection modules, etc.
Switching devices
The main devices used in the aforementioned bays include:
- GTR1, GTR 2, GTR 2V type switch disconnectors (ZPUE)
- GTR 4, GTR 4W type disconnectors (ZPUE)
- circuit breakers by leading manufacturers
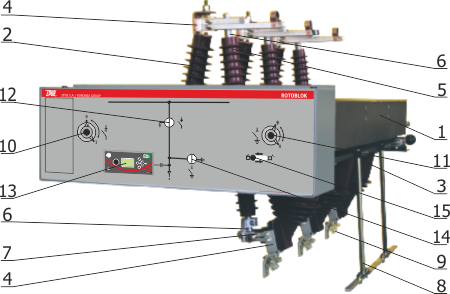
1 - galvanized steel frame
2,3 - resin insulators
4 - fixed contacts
5 - primary isolating shaft
6 - mobile contacts
7 - arc-quenching contact
8 - lower grounding switch
9 - grounding switch contact
10 - switch disconnector socket
11 - grounding switch socket
12 - switch disconnector position indicator
13 - voltage indicator
14 - grounding switch position indicator
15 - door interlock leaver
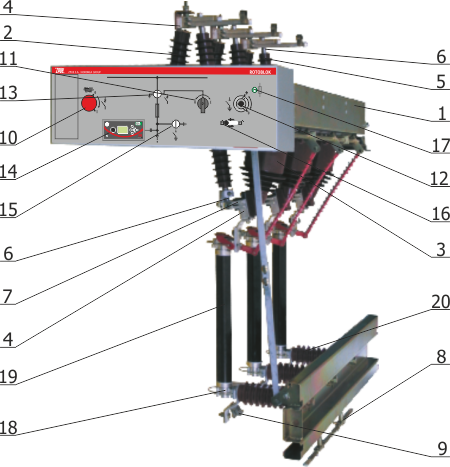
1 - zinc-coated steel frame
2,3 - resin insulators
4 - fixed contacts
5 - main insulating shaft
6 - moving contacts
7 - arcing moving contact
8 - lower earthing switch
9 - earthing switch contact
10 - charging socket and charging indicator
11 - “on”/“off” switch
12 - earthing switch socket
13 - switch disconnector position indicator
14 - voltage indicator
15 - earthing switch position indicator
16 - door interlock lever
17 - fuse link position indicator
18 - fuse base
19 - fuse link
20 - post insulator or capacitive voltage divider
Line feederwith manual drive

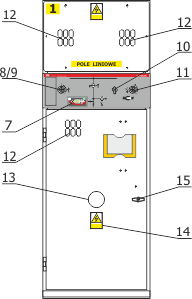
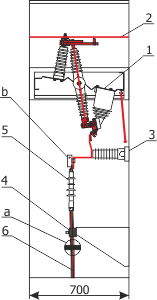
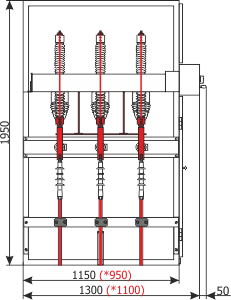
Standard equipment | |||
Device name | Type | Amount | |
1. | Switch disconnector with a lower earthing switch | GTR 1 or GTR 2 | 1 |
2. | Busbar circuit | P 40x5 / P 40x10 | 3 |
3. | Capacitive voltage divider | 3 | |
4. | Cable clamp | UKZ | 3 |
5. | Cable termination | 3 | |
6. | Cable | 3 | |
7. | Neon voltage indicator operating with the capacitive voltage divider | 1 | |
8. | Switch disconnector socket (for GTR 1) | 1 | |
9. | Charging socket and indicator (for GTR 2) | 1 | |
10. | “On”/“off” switch (for GTR 2) | 1 | |
11. | Earthing switch socket | 1 | |
12. | Inspection window | 1 | |
13. | Window which allows the use of a torch to check the position of contacts in case of a lighting failure |
3 | |
14. | Warning plate | 1 | |
15. | Door handle | 1 |
Additional equipment at the customer's request | ||
a | Short-circuit current indicator attached by cable | 1 |
b | Short-circuit current indicator attached by busbar | 3 |
Line feeder with motor drive
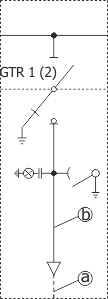
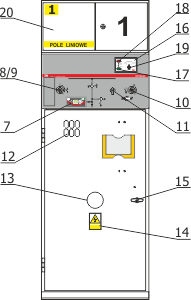
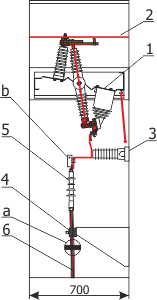
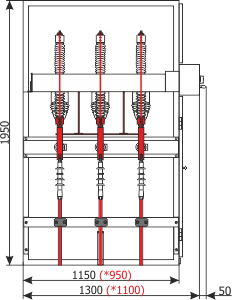
Standard equipment | |||
Device name | Type | Amount | |
1. | Switch disconnector with a lower earthing switch and motor drive adapted for remote control via cables or via radio | GTR 1M or GTR 2M | 1 |
2. | Busbar circuit | P 40x5 / P 40x10 | 3 |
3. | Capacitive voltage divider | 3 | |
4. | Cable clamp | UKZ | 3 |
5. | Cable termination | 3 | |
6. | Cable | 3 | |
7. | Neon voltage indicator operating with the capacitive voltage divider | 1 | |
8. | Switch disconnector socket (for GTR 1M) | 1 | |
9. | Charging socket and indicator (for GTR 2M) | 1 | |
10. | “On”/“off” switch (for GTR 2M) | 1 | |
11. | Earthing switch socket | 1 | |
12. | Inspection window | 1 | |
13. | Window which allows the use of a torch to check the position of contacts in case of a lighting failure | 3 | |
14. | Warning plate | 1 | |
15. | Door handle | 1 | |
16. | Control panel for motor drive | 1 | |
17. | “Close” button | 1 | |
18. | “Open” button | 1 | |
19. | Operation mode selection switch | 1 | |
20. | Auxiliary circuits compartment | 1 |
Additional equipment at the customer's request | ||
a | Short-circuit current indicator attached by cable | 1 |
b | Short-circuit current indicator attached by busbar | 3 |
Transformer feeder design
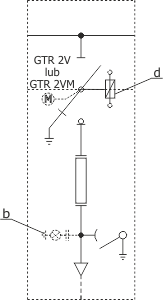
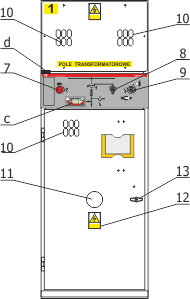
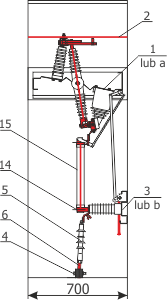

Standard equipment | |||
Device name | Type | Amount | |
1. | Fuse switch disconnector with earthing switch | GTR 2V | 1 |
2. | Busbar circuit | P 40x5 / P 40x10 | 3 |
3. | Post insulator | 3 | |
4. | Cable clamp | UKZ | 3 |
5. | Cable termination | 3 | |
6. | Cable | 3 | |
7. | Charging socket and indicator | 1 | |
8. | “On”/“off” switch | 1 | |
9. | Earthing switch socket | 1 | |
10. | Inspection window | 1 | |
11. | Window which allows the use of a torch to check the position of contacts in case of a lighting failure | 3 | |
12. | Warning plate | 1 | |
13. | Door handle | 1 | |
14. | Fuse base which forms an integral part of the switch disconnector | 1 | |
15. | Fuse link | 1 |
Additional equipment at the customer's request | |||
a | Fuse switch disconnector with earthing switch and motor drive | GTR 2VM | 1 |
b | Capacitive voltage divider | 3 | |
c | Neon voltage indicator operating with the capacitive voltage divider | 1 | |
d | Tripping coil | 1 | |
e | Gland for cable entry with the use of a tripping coil | 1 | |
Note! The earthing switch in the switch disconnector earths the lower part of the fuse link. |
Tripping coil operation in a transformer bay with gas-flow protection or thermal protection of the transformer
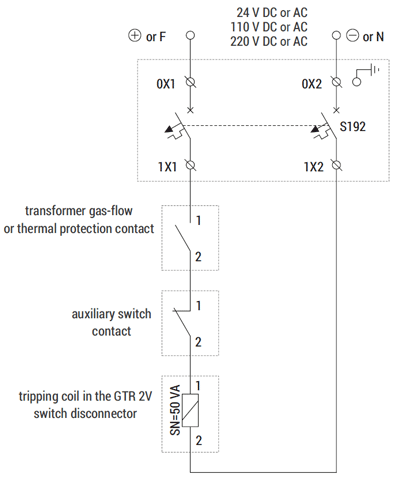
Note!
Cable cross-section and protection currents should be selected according to the tripping coil supply voltage.
Bus coupler unit design
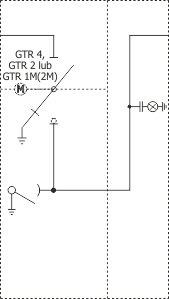

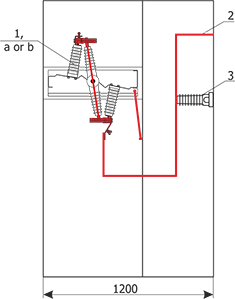
Standard equipment | |||
Device name | Type | Amount | |
1. | Disconnector with a lower earthing switch | GTR 4 | 1 |
2. | Busbar circuit | P 40x5 / P 40x10 | 3 |
3. | Post insulator or capacitive voltage divider | 3 | |
4. | Neon voltage indicator operating with the capacitive voltage divider | 1 | |
5. | Disconnector socket | 1 | |
6. | Earthing switch socket | 1 | |
7. | Inspection window | 1 | |
8. | Window which allows the use of a torch to check the position of contacts in case of a lighting failure | 3 | |
9. | Warning plate | 1 | |
10. | Door handle | 1 |
Additional equipment at the customer's request | |||
a | Switch disconnector with a lower earthing switch | GTR 2 | 1 |
b | Switch disconnector with a lower earthing switch and motor drive | GTR 1M or GTR 2M | 1 |
Note! The construction of a bus coupler bay without a lower earthing switch is possible |
Desing of transformer feeder type RWT
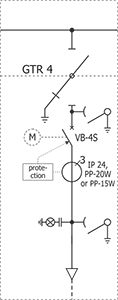
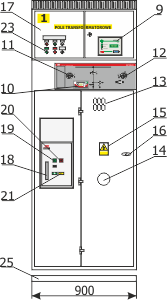
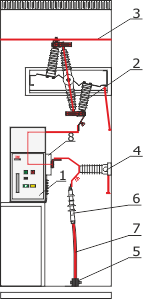
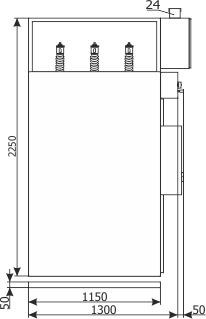
Standard equipment | |||
Device name | Type | Amount | |
1. | Circuit breaker | 1 | |
2. | Disconnector with a lower earthing switch | GTR 4 | 1 |
3. | Busbar circuit | P 40x5 / P 40x10 | 3 |
4. | Capacitive voltage divider | 3 | |
5. | Cable clamp | UKZ | 3 |
6. | Cable termination | 3 | |
7. | Cable | 3 | |
8. | Current transformer operating with the protection system | IP 24 / PP-20W / PP-15W | 3 |
9. | Protection system | Mupasz / REF MiCOM | 1 |
10. | Neon voltage indicator operating with the capacitive voltage divider | 1 | |
11. | Disconnector socket | 1 | |
12. | Earthing switch socket | 1 | |
13. | Inspection window | 1 | |
14. | Window which allows the use of a torch to check the position of contacts in case of a lighting failure | 1 | |
15. | Warning plate | 1 | |
16. | Door handle | 1 | |
17. | Auxiliary circuits compartment | 1 | |
18. | Charging socket | 1 | |
19. | “ON” button | 1 | |
20. | “OFF” button | 1 | |
21. | Charging indication | 1 | |
23. | Control switches and lamps | 1 | |
24. | Cable tray | 1 | |
25. | Load-bearing frame | 1 |
Desing of bus cupler unit type RWS
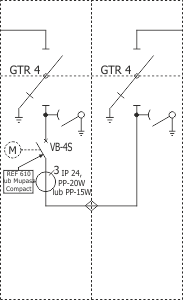
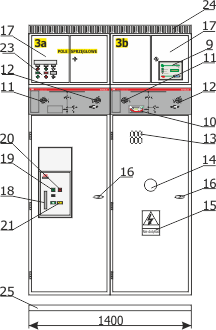
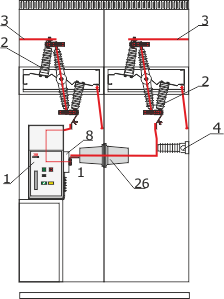

Standard equipment | |||
Unit | Type | Amount | |
1. | Circuit breaker | 1 | |
2. | Disconnector with a lower earthing switch | GTR 4 | 1 |
3. | Busbar circuit | P 40x5 / P 40x10 | 3 |
4. | Capacitive voltage divider | 3 | |
8. | Current transformer operating with the protection system | IP 24 / PP-20W / PP-15W | 3 |
9. | Protection system | Mupasz / REF MiCOM | 1 |
10. | Neon voltage indicator operating with the capacitive voltage divider | 1 | |
11. | Disconnector socket | 1 | |
12. | Earthing switch socket | 1 | |
13. | Inspection window | 1 | |
14. | Window which allows the use of a torch to check the position of contacts in case of a lighting failure | 1 | |
15. | Warning plate | 1 | |
16. | Door handle | 1 | |
17. | Auxiliary circuits compartment | 1 | |
18. | Charging socket | 1 | |
19. | „ON” button | 1 | |
20. | „OFF” button | 1 | |
21. | Charging indication | 1 | |
23. | Control switches and lamps | 1 | |
24. | Cable tray | 1 | |
25. | Load-bearing frame | 1 | |
26. | Insulating bushing | 1 |
Control circuits panel: “auxiliary circuits compartment”
The auxiliary circuits compartment (17) contains control strips, protection units, control & metering devices and buttons. Based on documentation provided by the customer, the manufacturer determines the position of the auxiliary circuit devices in the switchgear. Auxiliary circuit leads and cables are placed in the compartment in cable trays, and exit the compartment through glands. The auxiliary circuits in the remaining compartments run in protection tubes. The bypass circuits between adjacent bays run in trays. It is recommended that auxiliary circuit cables are run from individual distribution bays to the control room in a cable duct or on cable ladders installed on the walls.
Construction method for a cable duct under the Rotoblok type MV switchgears
Figures 1, 2, 3 present a cable duct construction proposal. The cable bending radius (which depends on its outside diameter, according to PBUE) should taken into account when establishing the dry and oil cables duct depth. It is possible to avoid or reduce the depth of the cable duct by using a raised base or a raised floor.
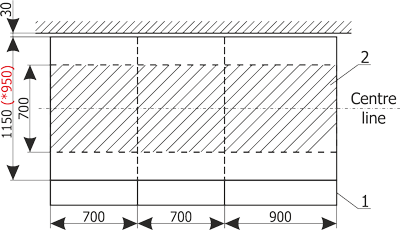
Note!: Minimum distance from the wall 30 mm
1) Example bays with a width of 700, 700, 900 mm (respectively, from the left)
2) Duct under the switchgear.
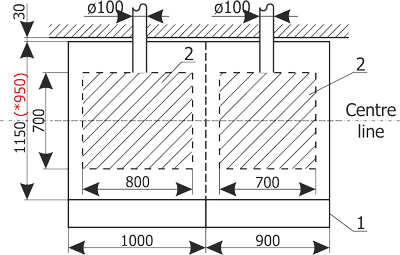
* - Rotoblok 17,5 kV switchgear depth
Note!: Minimum distance from the wall 30 mm
1) Example bays with a width of 1000, 900 mm (respectively, from the left)
2) Duct under the switchgear.
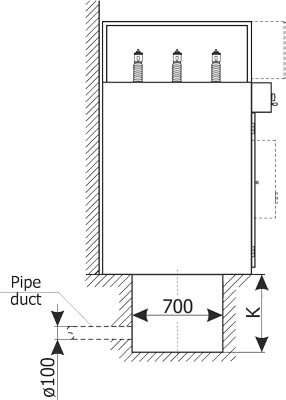
Cable cross-section (mm2) | Bending radius (mm) | Duct depth K (mm) |
50 | 370 | 400 |
70 | 400 | 430 |
95 | 440 | 470 |
120 | 470 | 500 |
150 | 500 | 550 |
185 | 540 | 600 |
240 | 590 | 700 |
Rotoblok switchgear cable connections
Switch disconnector and circuit breaker feeder bays | ||||
Cable type | Cable termination | |||
Manufacturer | Type | Cable cross-section [mm2] | ||
Single core, with plastic insulation e.g. YHAKXs, YHKX, XUHAKXs, XRUHKs, ... |
CELLPACK | CHE-I 24kV | 25-150 | |
70-240 | ||||
CAE-I 24kV | 35-120 | |||
70-240 | ||||
CAESK-I 24kV | 70-150 | |||
120-240 | ||||
Nexans (EUROMOLD) | ITK224 (stretch sleeve) | 25-240 | ||
AIP20 (slip-on) | 25-120 | |||
AIS20 (slip-on) | 70-300 | |||
AIN20 (slip-on) | 25-1200 | |||
24MONOi1 (shrink sleeve) | 25-240 | |||
TYCO ELECTRONIC | Rated voltage | Typ (stretch sleeve) | ||
6/10 | POLT-12xxx | 25-1200 | ||
8,7/15 i 12/20 | POLT-24xxx | 25-800 | ||
18/30 | POLT-42xxx | 35-800 |
*) Note: The manufacturer should be consulted regarding the manner of connection of cables and used terminations
Transformer bays | |
Single core, with plastic insulation e.g. YHAKXs, YHKX, XUHAKXs, XRUHKs, ... |
As in feeder bays |
Tri-core oil-filled with paper insulation saturated with non-running saturant and common coating, e.g.: HAKnFta, KnY, KnFTA, ... |
The manufacturer should be consulted regarding the manner of connection of cables and used terminations |
Note:
In all cases a cable duct is required under the switchgears. As an option, the switchgear may be placed on a raised base or on a raised floor. In case other type of terminations is used, please contact the manufacturer.
Various types of Rotoblok switchgear units
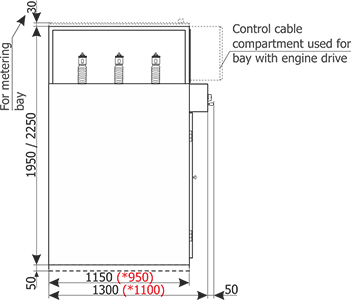
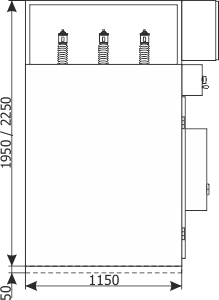
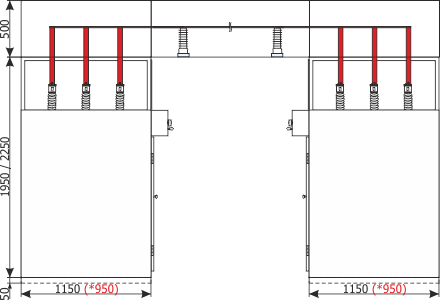
* - Rotoblok switchgear 17,5 kV depth
Note:
Figures shown on subsequent pages are only an example of bay equipment. It is possible to adapt the bay configuration to specific requirements of the end user. In this case manufacturer should be asked to provide drawings.
RL1 (line feeder)
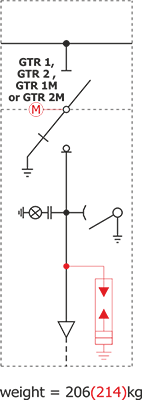
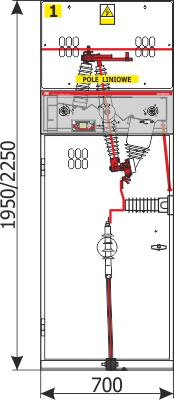
Note:
Optional equipment was marked with red on the electrical diagram.
1) It is possible to design the unit in mirrored version
2) It is possible to design the bus coupler unit without a lower earthing switch
RL4 (line feeder with metering)
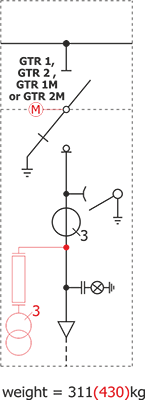
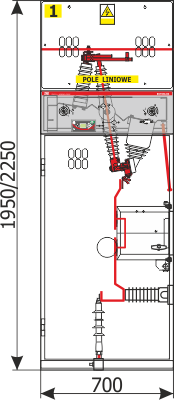
Note:
Optional equipment was marked with red on the electrical diagram.
1) It is possible to design the unit in mirrored version
2) It is possible to design the bus coupler unit without a lower earthing switch
RT1 (transformer feeder)
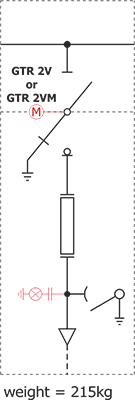
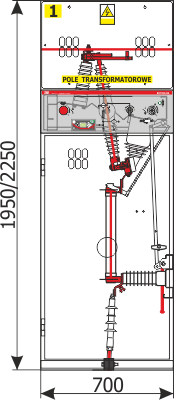
Note:
Optional equipment was marked with red on the electrical diagram.
1) It is possible to design the unit in mirrored version
2) It is possible to design the bus coupler unit without a lower earthing switch
RS1L1) (bus coupler unit with disconnector or switch disconnector on the left side)
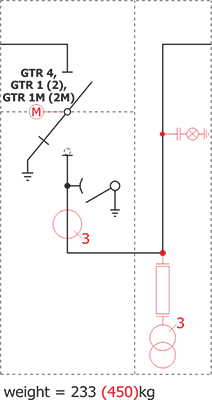

Note:
Optional equipment was marked with red on the electrical diagram.
1) It is possible to design the unit in mirrored version
2) It is possible to design the bus coupler unit without a lower earthing switch
RS4 (bus coupler unit with disconnector or switch disconnector on the left side)
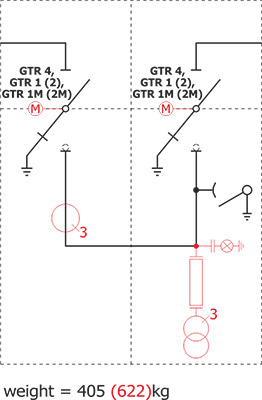

Note:
Optional equipment was marked with red on the electrical diagram.
1) It is possible to design the unit in mirrored version
2) It is possible to design the bus coupler unit without a lower earthing switch
RP1 (metering unit)
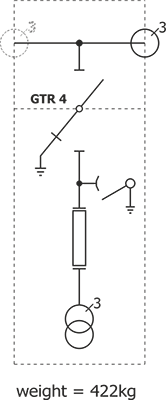
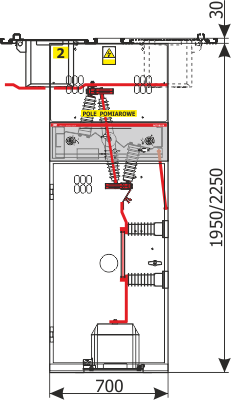
Note:
Optional equipment was marked with red on the electrical diagram.
1) It is possible to design the unit in mirrored version
2) It is possible to design the bus coupler unit without a lower earthing switch
RO1 (lightning arrester unit)
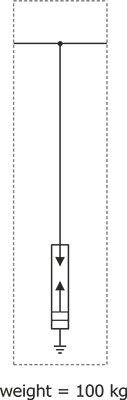
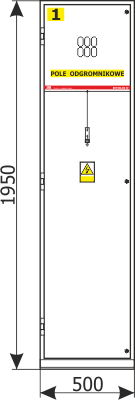
Note:
Optional equipment was marked with red on the electrical diagram.
1) It is possible to design the unit in mirrored version
2) It is possible to design the bus coupler unit without a lower earthing switch
RŁ2 (Incoming cable-connection feeder)
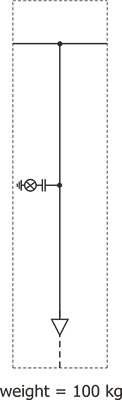
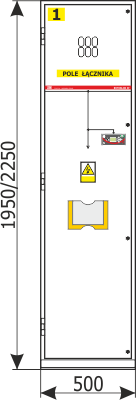
Note:
Optional equipment was marked with red on the electrical diagram
Rtpwł4 (auxiliary transformer unit)
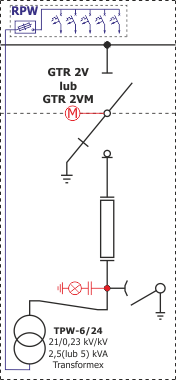

Note:
Optional equipment was marked with red on the electrical diagram
RTpwł 25kVA + RT1 (auxiliary transformer unit - max. power 25 kVA)
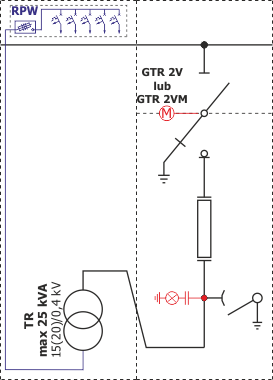

Note:
Optional equipment was marked with red on the electrical diagram
RWT (circuit breaker transformer bay)

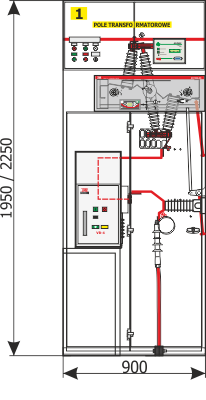
Note:
Optional equipment was marked with red on the electrical diagram
RWT3 (circuit breaker transformer feeder)
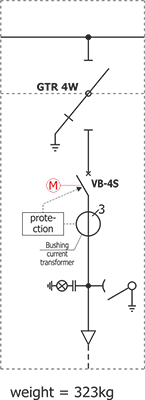
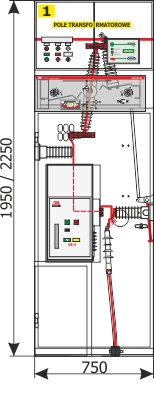
Note:
Optional equipment was marked with red on the electrical diagram
RWTp14 (circuit breaker transformer feeder with voltage measurement)
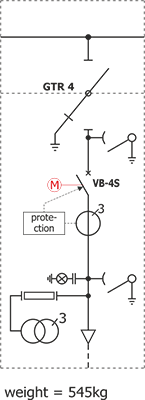
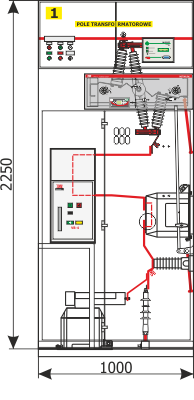
Note:
Optional equipment was marked with red on the electrical diagram